
Welcome to the 9th annual list of intersectional feminist media recommendations from the past year! 2023 started off a bit slow with little to recommend in the first few months. The year seemed slower than usual in terms of intersectional feminist content, but I put together some of the things that stood out and some even were inspiring.

Academy Awards (March 2023) – Michelle Yeoh was the first woman who identifies as Asian nominated and won for Best Actress. To date, only four Asian actors received acting nominations: Hong Chau, Stephanie Hsu, and winners Ke Huy Quan and Yeoh. Everything Everywhere All at Once led the ceremony with eleven nominations and seven wins, including Best Picture, Best Director and Best Original Screenplay for Daniel Kwan and Daniel Scheinert, and three of the four acting awards.
The Diplomat (created by Debora Cahn, Netflix, April 2023) – political suspense drama, created by Debora Cahn (who worked on The West Wing, Grey’s Anatomy, and Homeland) about the new US ambassador to the UK, Kate Wyler (played by Keri Russell) as she has to defuse international conflicts, constantly cleaning up messes that less capable men cause, and survive her marriage to fellow career diplomat and former ambassador Hal Wyler (played by Rufus Sewell). It’s fun to watch women being really in charge even when men are in top positions of power, but also frustrating to see their challenges when they are always right, but no one listens.

Slip (created by Zoe Lister-Jones, The Rocu Channel, April 2023) – Restless in her marriage, Mae (played by Zoe Lister-Jones, who is best known for the sitcom Life in Pieces 2015-2019) finds herself in parallel universes (whenever she has an orgasm with a new person), married to different people and trying to find a way back to her partner, and, ultimately, to herself. Clever and original.
Monsters: A Fan’s Dilemma (Claire Dederer, April 2023) – this book expands on Claire Dederer’s instantly viral Paris Review essay, “What Do We Do with the Art of Monstrous Men?” Can we love the work of artists such as Ernest Hemingway, Sylvia Plath, Miles Davis, Roman Polanski, Woody Allen or Pablo Picasso? She explores the audience’s relationship with artists, asking: how do we balance our undeniable sense of moral outrage with our equally undeniable enjoyment of the work? Is male monstrosity the same as female monstrosity? And if an artist is also a mother, does one identity inexorably, and fatally, interrupt the other? Does genius deserve special dispensation? Does art have a mandate to depict the darker elements of the psyche? Highly relevant in light of #metoo and the backlash on abortion, women’s rights, and LGBTQ+ rights, this book can incite a long-awaited conversation about whether and how we can separate artists from their art.
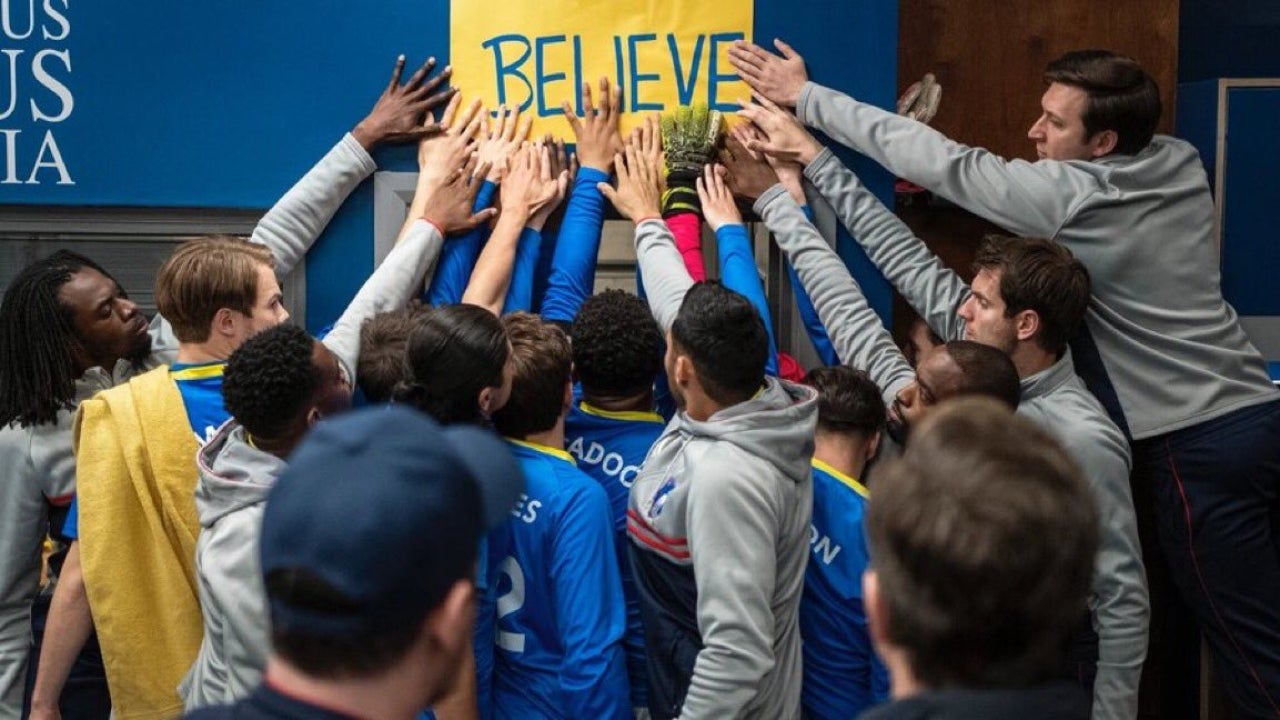
Ted Lasso, Season 3 (developed by Jason Sudeikis, Bill Lawrence, Brendan Hunt, and Joe Kelly, Apple+ May 2023) – the third and final season rounds out the story of how to build not just a team, but a community based on kindness. Hopefully there will be a spin-off that foregrounds all the female characters.

Survival of the Thickest (Netflix, July 2023) – created by the comedian Michelle Buteau, the show is a smart, funny, and entertaining portrayal of Mavis Beaumont, a plus-sized woman of colour, newly single and rebuilding her life as a struggling stylist. Clever and inspirational in how it deals with race, relationships, body positivity, friendships, and precarity of work in cultural industries, the show is just fun to watch.
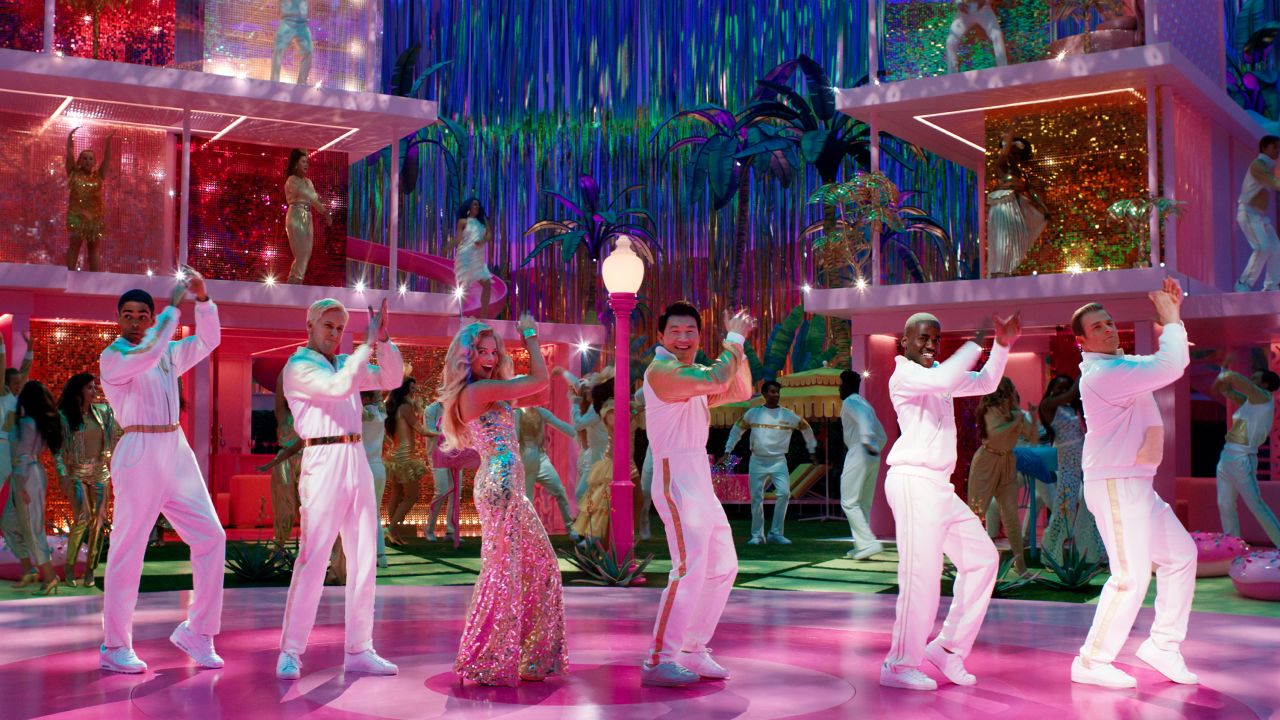
Barbie (dir. by Greta Gerwig, July 2023) – This is a white-feminism film for old people and for dudes who are still not sure what to be beyond their masculinity crisis. While the music and dance scenes are a great spectacle, the plot and feminist messages of this film are at least one generation behind intersectional, queer, and inclusive wokeness of the newer generations. It became the highest-grossing film made by a female director (despite censorship and bans in some countries for LGBTQ+ themes). Overall, entertaining and funny, but not fully up to date in terms of intersectional feminism.
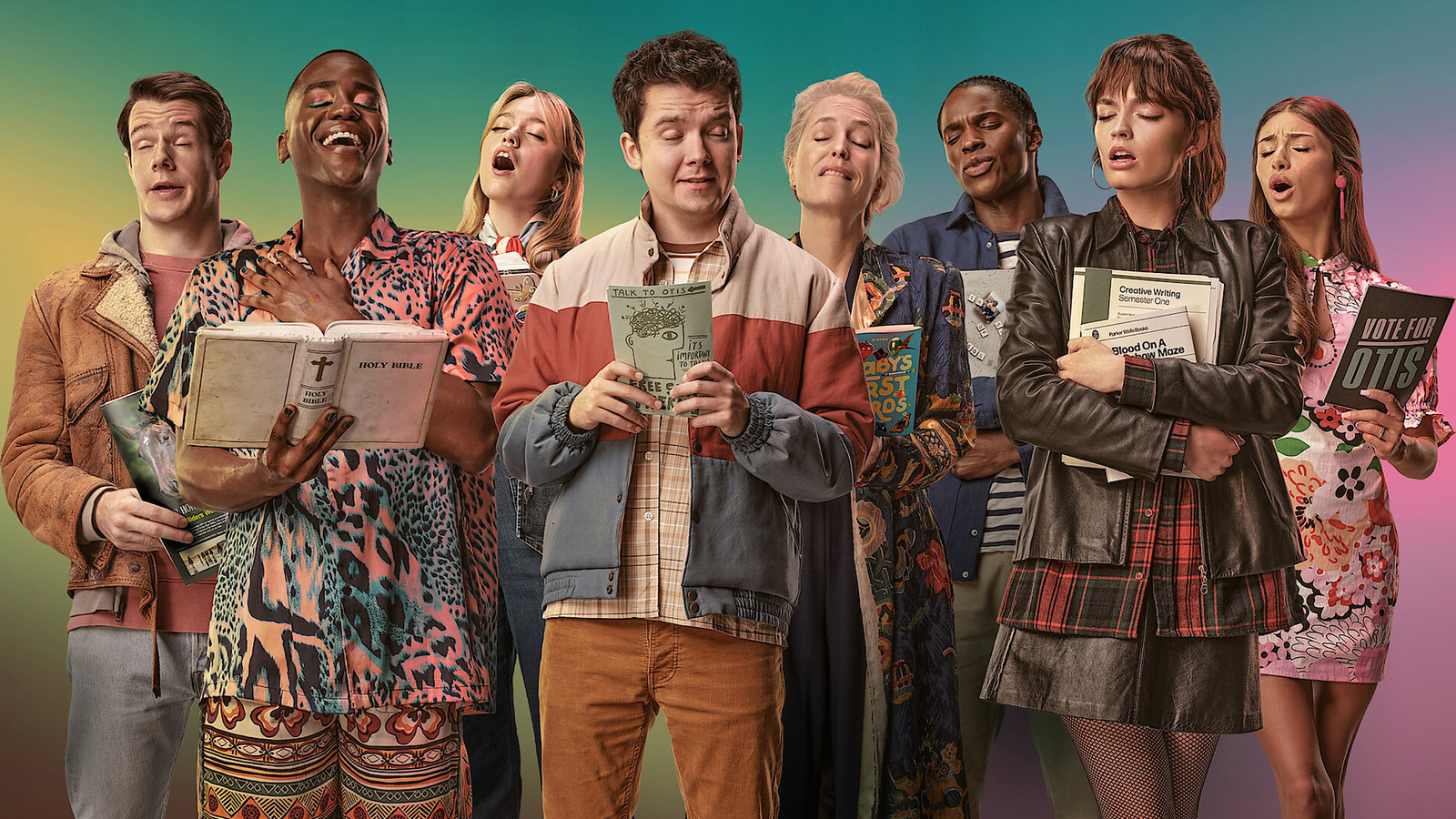
Sex Education, Season 4 (created by Laurie Nunn, Netflix, September 2023) – The fourth and final season presents a colourful utopia for inclusivity in a school run by diverse and woke students, who have a gossip coin jar, practice kindness “not as a brand, but because it’s the right thing to do,” and have two student sex therapist to help them navigate their personal and sexual escapades.
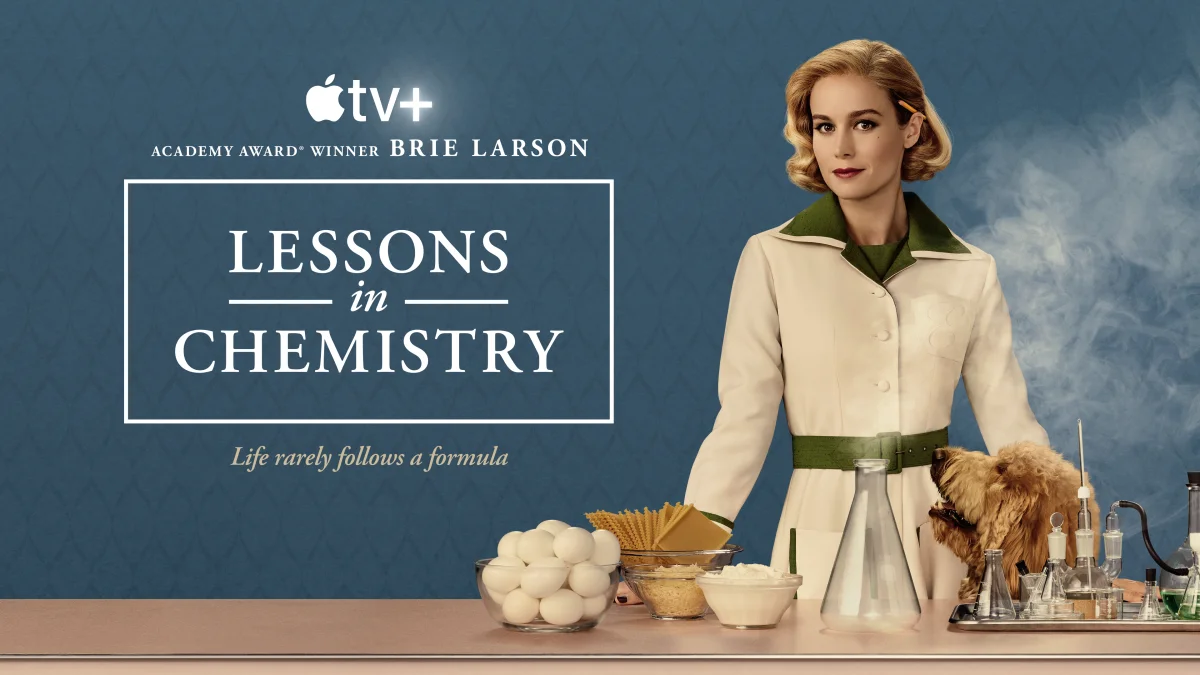
Lessons in Chemistry (based on a book by Bonnie Garmus, developed by Lee Eisenberg, October – November 2023) – television miniseries stars Brie Larson as chemist Elizabeth Zott who begins hosting her own feminist cooking show in 1960s America, despite tragic setbacks in her career and personal life, and despite blatant patriarchal sexism, professional sabotage, and even violence. A refreshing reminder of what women had to put up with just a few generations ago, and how much resilience they needed to overcome all the obstacles placed in their way.
For previous years’ lists, please see these links: Feminism 2015, Feminism 2016, Feminism 2017, Feminism 2018, Feminism 2019, Feminism 2020, Feminism 2021, and Feminism 2022.
Thank you for reading!